1.Vacuum Metalizing
A type of physical deposition process. In a vacuum environment, argon gas is injected, which strikes the target material, causing the target to break into molecules. These molecules are then adsorbed by the conductive product, forming a uniform and smooth metal-like surface layer.
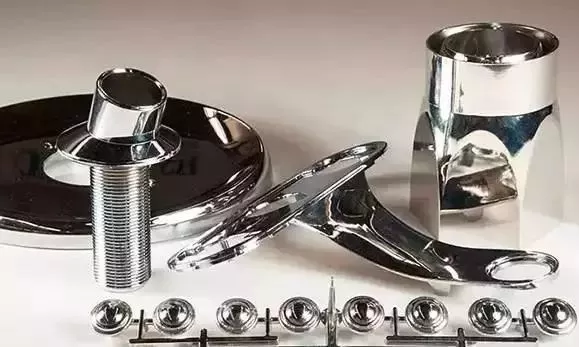
Typical Products:
Reflective coatings, surface treatments for consumer electronics, and insulation panels.
Production Volume Suitability:
Suitable for both single-piece and mass production.
Quality:
High-quality, high-gloss finish with a protective layer on the product surface.
Speed:
Moderate production speed, 6 hours per cycle (including painting).
Applicable Materials
- Many materials can undergo vacuum plating, including metals, soft and hard plastics, composites, ceramics, and glass. The most commonly used material for surface plating is aluminum, followed by silver and copper.
- Natural materials are not suitable for vacuum plating, as the moisture in natural materials can affect the vacuum environment.
Process Cost
Vacuum electroplating is highly dependent on manual operations. During the process, workpieces need to be sprayed, loaded, unloaded, and resprayed. Therefore, labor costs are relatively high but also depend on the complexity and quantity of the workpieces.
Environmental Impact
Vacuum electroplating has minimal environmental pollution, similar to the impact of spraying.
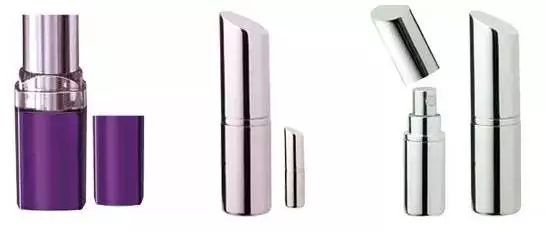
2.Electropolishing
The workpiece to be polished serves as the anode, and an insoluble metal serves as the cathode. Both electrodes are immersed in an electrolytic tank. By applying direct current, selective anodic dissolution occurs, removing fine burrs and increasing the brightness of the workpiece surface.
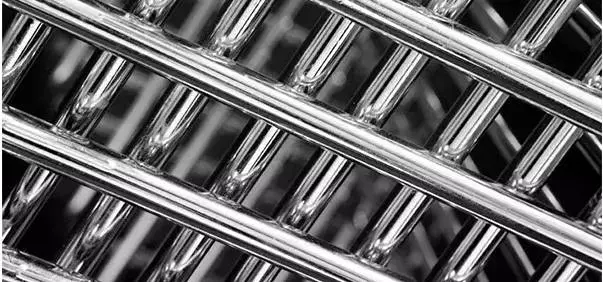
Typical Products:
Architectural structures, food processing and storage equipment, medical and pharmaceutical components.
Suitable Production Volume:
From single pieces to mass production.
Quality:
High surface brightness, smoothness, and hygiene.
Speed:
Medium production speed, 5–30 minutes per cycle.
Applicable Materials
- Most metals can undergo electrolytic polishing, most commonly stainless steel (especially austenitic nuclear-grade stainless steel).
- Different materials cannot be electrolytically polished simultaneously and should not be placed in the same electrolyte.
Process Cost
The entire electrolytic polishing process is mostly automated, resulting in very low labor costs.
Environmental Impact
Electrolytic polishing uses less harmful chemicals and requires minimal water throughout the process. It also extends the properties of stainless steel, delaying corrosion.
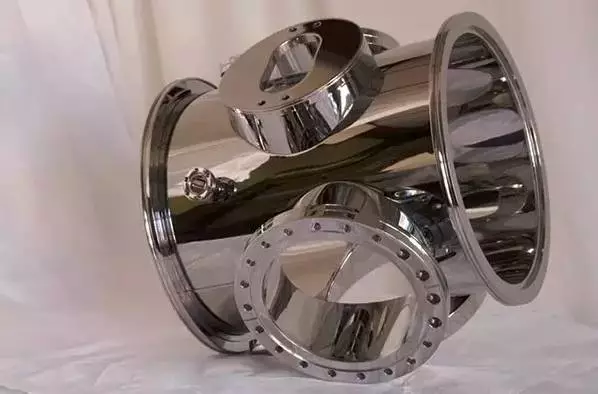
3.Photoetching
Also known as photolithography, it uses photographic methods to create a photoresist image that protects the surface. On metals, plastics, and other materials, chemical etchants are used to create surface textures.
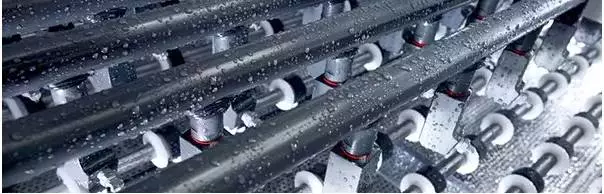
Typical Products:
Jewelry, nameplates, and trophies.
Suitable Production Volume:
From single pieces to mass production.
Quality:
Extended exposure and chemicals can achieve photoetching surface effects.
Speed:
Medium production speed (50–100 microns per 5 minutes).
Applicable Materials
- Most metals are suitable, including stainless steel, mild steel, aluminum, brass, nickel, tin, copper, and silver. Aluminum etches the fastest, while stainless steel etches the slowest.
- Glass and ceramics are also suitable but require different photoresists and chemicals.
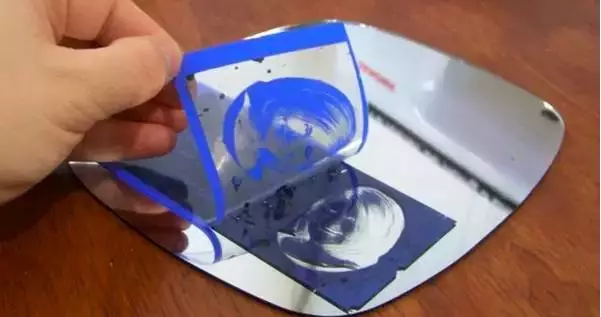
Process Cost
- Low mold costs.
- Moderate labor costs.
Environmental Impact
Metal waste from photoetching must be properly recycled. Chemicals used include ferric chloride and caustic soda, both harmful substances requiring protective handling.
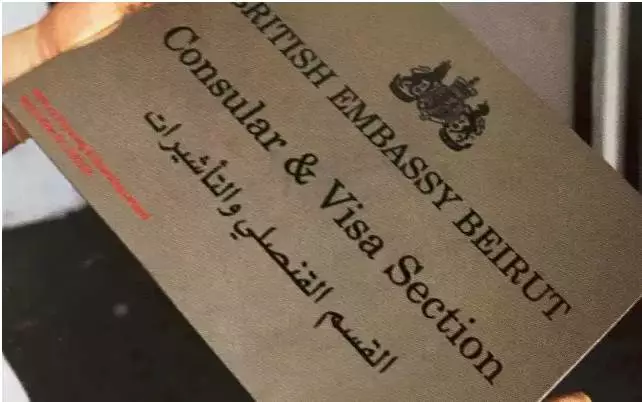
4.Pad Printing
A printing technique that can print text, graphics, and images on irregularly shaped objects, becoming an important method in special printing.
Typical Products:
Interior parts of vehicles, consumer electronics, sports equipment.
Suitable Production Volume:
From single pieces to mass production.
Quality:
Capable of clear printing details, even on uneven surfaces.
Speed:
Single print time of 1–5 seconds.
Applicable Materials
Almost all materials can be pad printed except those softer than the silicone pad, such as PTFE.
Process Cost
- Low mold costs.
- Low labor costs due to machine processing.
Environmental Impact
Limited to solvent-based inks containing harmful chemicals, leading to significant environmental impact.
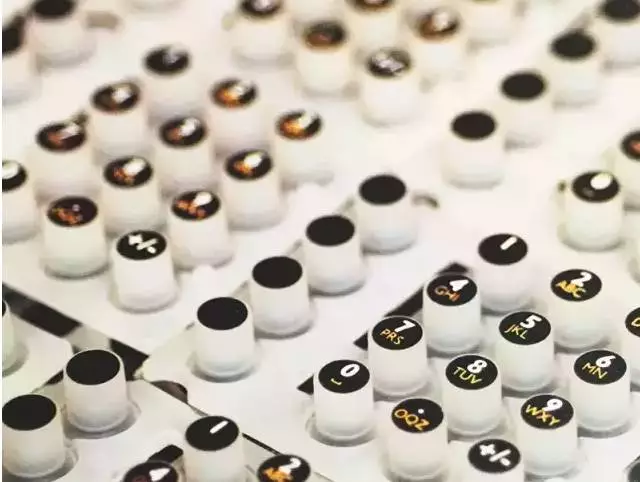
5.Galvanizing
A surface treatment technique where a layer of zinc is applied to the surface of steel or iron alloy materials for aesthetics and rust prevention. The zinc layer acts as an electrochemical protective layer to prevent metal corrosion, mainly through hot-dip galvanizing and electro-galvanizing.
Typical Products:
Construction materials, bridges, vehicles, furniture.
Suitable Production Volume:
From single pieces to mass production.
Quality:
Excellent protective layer; appearance largely depends on the quality of the steel.
Speed:
Fast, approximately 10 minutes per cycle.
Applicable Materials
Only suitable for steel and iron due to reliance on metallurgical bonding technology.
Process Cost
- No mold costs, short cycles, relatively low cost.
- Moderate labor costs, as surface quality depends greatly on manual pre-treatment.
Environmental Impact
Extends the service life of steel parts by 40–100 years, preventing rust and corrosion, which positively impacts environmental protection. Galvanized parts can be recycled without producing chemical or physical waste.
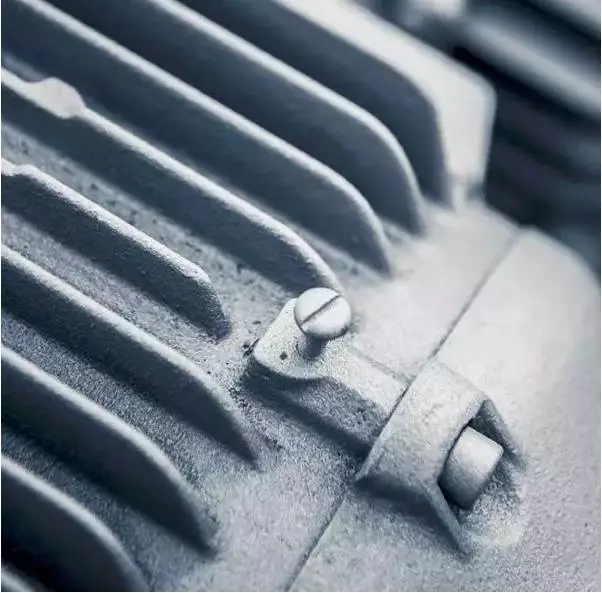
6.Electroplating
Uses electrolysis to attach a metal film to the surface of parts, preventing oxidation, improving wear resistance, conductivity, reflectivity, and corrosion resistance, and enhancing aesthetics. Many coins have electroplated outer layers.
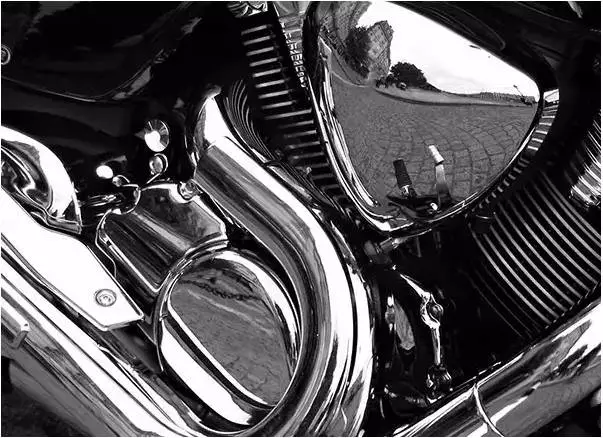
Typical Products:
Vehicles, consumer electronics, furniture, jewelry, silverware.
Suitable Production Volume:
From single pieces to mass production.
Quality:
Extremely high gloss, oxidation and corrosion resistance.
Speed:
Medium speed, depending on material type and coating thickness.
Applicable Materials
- Most metals can be electroplated, with varying purity and efficiency. Common metals include tin, chromium, nickel, silver, gold, and rhodium.
- ABS plastic is commonly used because it withstands the high temperatures of electroplating and bonds well with the plating layer.
- Nickel should not be used on products that contact skin due to toxicity.
Process Cost
- No mold costs but requires fixtures.
- Time cost depends on temperature and metal type.
- Labor cost ranges from medium to high, depending on product type.
Environmental Impact
Uses many toxic substances; requires professional handling to minimize environmental impact.
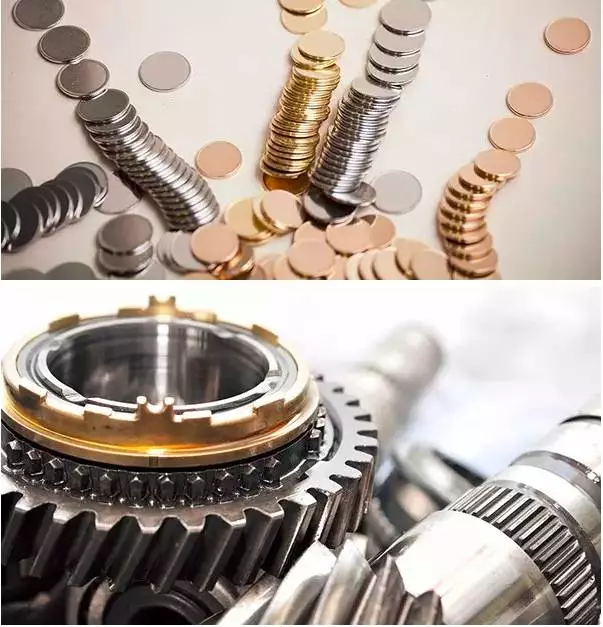
7.Powder Coating
A dry spraying method applied to metal workpieces via spraying or fluidized beds. Powder adheres electrostatically to the workpiece surface and forms a protective film upon drying.
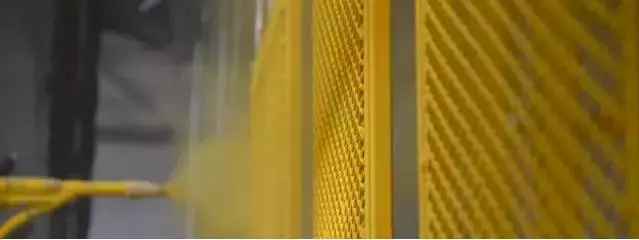
Typical Products:
Vehicles, construction materials, home appliances.
Suitable Production Volume:
From single pieces to mass production.
Quality:
Smooth and even surface coloring.
Speed:
Dependent on workpiece size and automation; drying takes at least 30 minutes.
Applicable Materials
Mainly used for aluminum and steel but also suitable for some plastics and glass.
Process Cost
- No mold costs, but equipment is expensive.
- Short time cost, with at least 30 minutes for drying.
- Very low labor costs.
Environmental Impact
Higher material utilization (up to 95%) due to electrostatic adsorption, reducing waste.
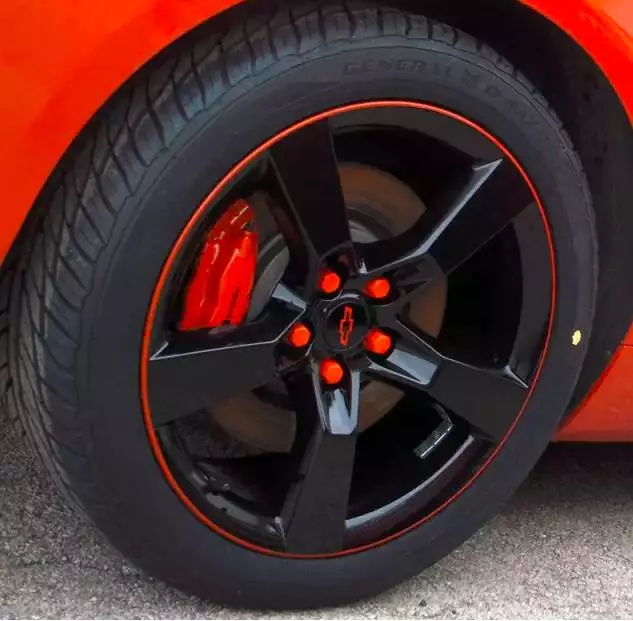
Hydro Transfer Printing
Uses water pressure to transfer patterns from transfer paper onto three-dimensional products. Its use is expanding with increasing demands for product packaging and surface decoration.
Typical Products:
Vehicles, consumer electronics, military products.
Suitable Production Volume:
Small to large batches.
Quality:
Accurate and clear surface textures with slight stretching.
Speed:
Fast, 10–20 cycles per hour.
Applicable Materials
All hard materials; commonly used on injection-molded and metal parts.
Process Cost
- No mold costs; fixtures needed to process multiple products simultaneously.
- Short time cost, generally less than 10 minutes per cycle.
Environmental Impact
More efficient use of printing coatings compared to spraying, reducing waste.
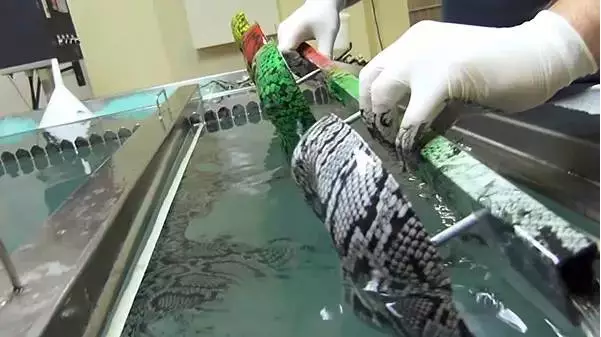
8.Screen Printing
Uses a squeegee to transfer ink through a mesh stencil onto a substrate, replicating the original design. Equipment is simple and cost-effective, with broad adaptability.
Typical Products:
Clothing, electronic products, packaging.
Suitable Production Volume:
From single pieces to mass production.
Quality:
Extremely high detail precision.
Speed:
Manual (1–5 cycles per minute), automated (1–30 cycles per minute).
Applicable Materials
Nearly all materials, including paper, plastics, metals, ceramics, and glass.
Process Cost
- Low mold costs; each color requires a separate stencil.
- Time and labor costs vary between manual and automated processes.
Environmental Impact
Light-colored inks have minimal impact, but inks containing PVC and formaldehyde require careful handling to prevent water pollution.
9.Anodic Oxidation
Mainly applied to aluminum, it uses electrochemical principles to form an Al2O3 (aluminum oxide) film on the surface, providing protection, decoration, insulation, and wear resistance.
Typical Products:
Electronics (phones, computers), mechanical parts, automotive and aircraft components, precision instruments, consumer goods, architectural decorations.
Suitable Production Volume:
From single pieces to mass production.
Quality:
Protective oxide film with special properties.
Speed:
Takes several tens of minutes.
Applicable Materials
Aluminum and aluminum alloys.
Process Cost
High water and electricity consumption; reducing auxiliary facilities can lower costs.
Environmental Impact
Not energy-efficient; production can emit gases harmful to the ozone layer.
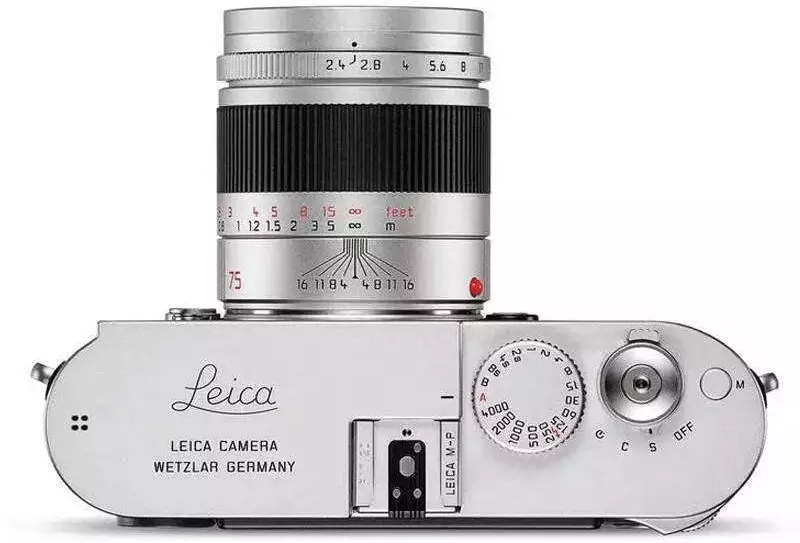
10.Electrophoresis
Charged particles move toward an electrode under an electric field.
Typical Products:
Automobiles, building materials, hardware, home appliances.
Suitable Production Volume:
Mass production.
Quality:
Products exhibit various colors while maintaining metallic luster and enhanced surface properties.
Speed:
Fast production speed.
Applicable Materials
Stainless steel, aluminum alloys, and similar materials.
Process Cost
Automated continuous operation with low labor costs and overall low cost.
Environmental Impact
Uses water-based solvents, reducing air pollution and eliminating fire hazards.
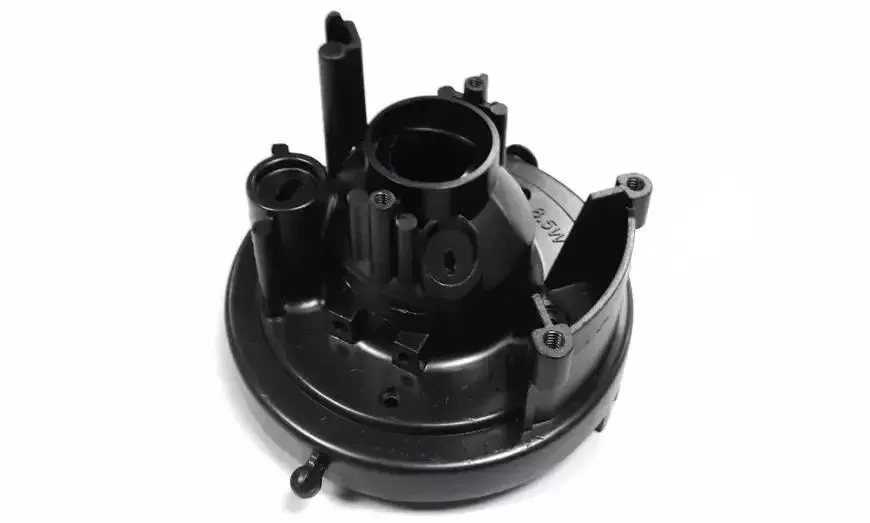
11.Micro-Arc Oxidation (MAO)
Also known as micro-plasma oxidation, it uses a combination of electrolyte and electrical parameters to grow a ceramic coating on metals like aluminum, magnesium, and titanium through instantaneous high-temperature and high-pressure arc discharge.
Typical Products:
Aerospace components, IT products.
Suitable Production Volume:
From single pieces to mass production.
Quality:
High surface hardness and excellent wear resistance.
Speed:
Fast processing speed.
Applicable Materials
Aluminum, magnesium, titanium, and their alloys.
Process Cost
High energy consumption and treatment costs due to high voltage and current density, limiting widespread application.
Environmental Impact
Electrolyte contains no toxic substances or heavy metals; high reuse rate minimizes environmental pollution.
12.Metal Brushing
A surface treatment that creates lines on a workpiece through grinding, providing a decorative effect. Types include straight, random, ripple, and spin patterns.
Typical Products:
Building materials like elevator panels, faucets, handles; kitchenware such as range hoods and sinks.
Suitable Production Volume:
From single pieces to mass production.
Quality:
Achieves a non-mirror metallic luster and can eliminate minor surface imperfections.
Speed:
Fast processing.
Applicable Materialse
Almost all materials can undergo metal brushing.
Process Cost
Simple methods and equipment with minimal material consumption; cost-effective with high economic benefits.
Environmental Impact
Pure metal products without paints or chemicals; non-flammable at high temperatures and emit no toxic gases, meeting fire safety and environmental requirements.
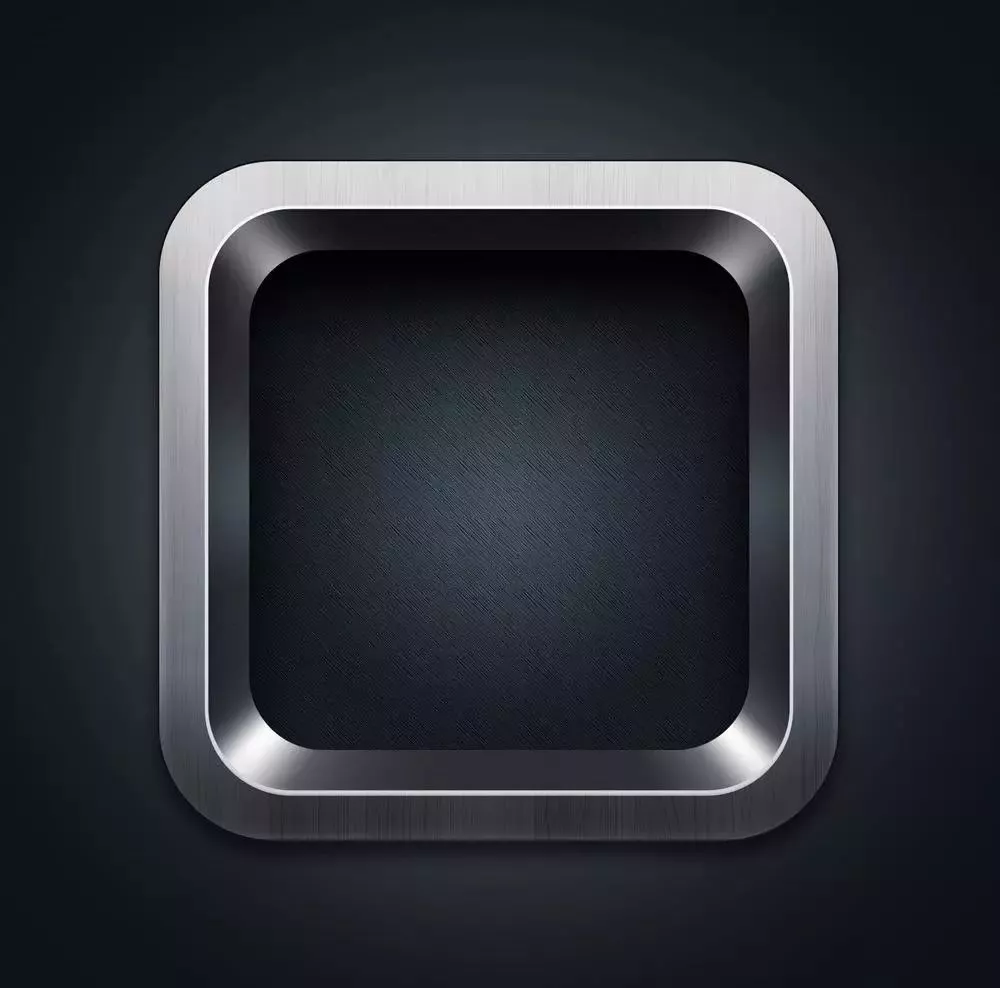
13.In-Mold Decoration
Involves placing a pre-printed film into a metal mold. Resin is injected to bond with the film, forming a single solidified product.
Typical Products:
Control panels for appliances, automotive dashboards, air conditioning panels, mobile phone cases/screens, washing machines, refrigerators.
Suitable Production Volume:
From single pieces to mass production.
Quality:
Suitable for complex images; products are wear-resistant and maintain vibrant colors over time.
Speed:
Rapid processing.
Applicable Materials
Plastic surfaces.
Process Cost
Reduces system and inventory costs by requiring only one mold. Highly automated production simplifies processes and reduces costs and labor.
Environmental Impact
Environmentally friendly technology that avoids pollution from traditional painting and electroplating methods.
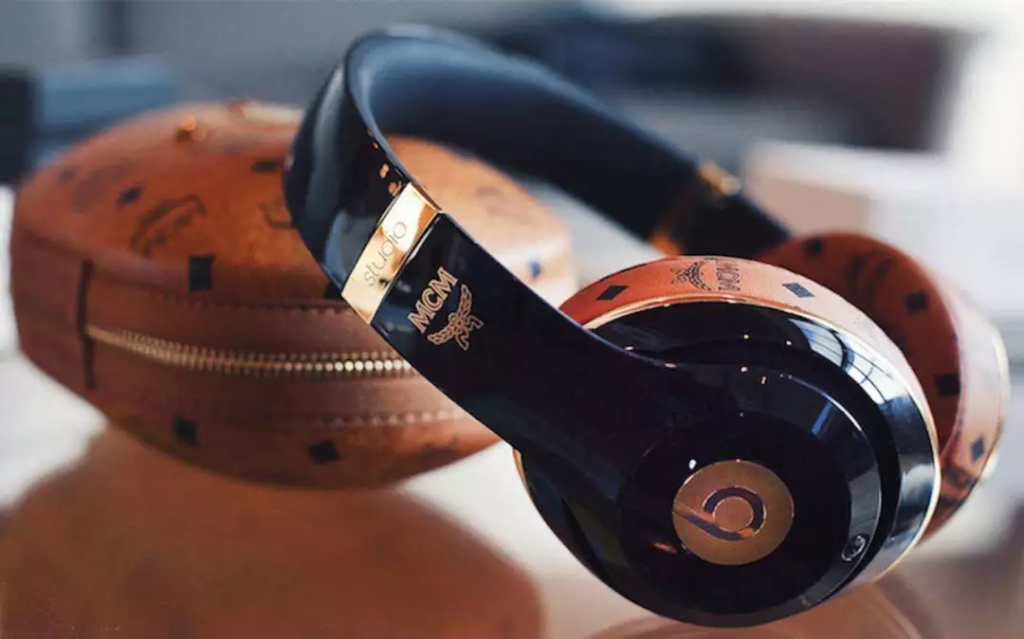
Contact us for expert support in custom machined parts. We’re dedicated to delivering high quality, precision, and quick turnaround for your projects.