Bearings typically consist of an inner ring, outer ring, rolling elements, and a cage. For sealed bearings, lubricants and seals (or dust covers) are also included. These components make up the entirety of a bearing.
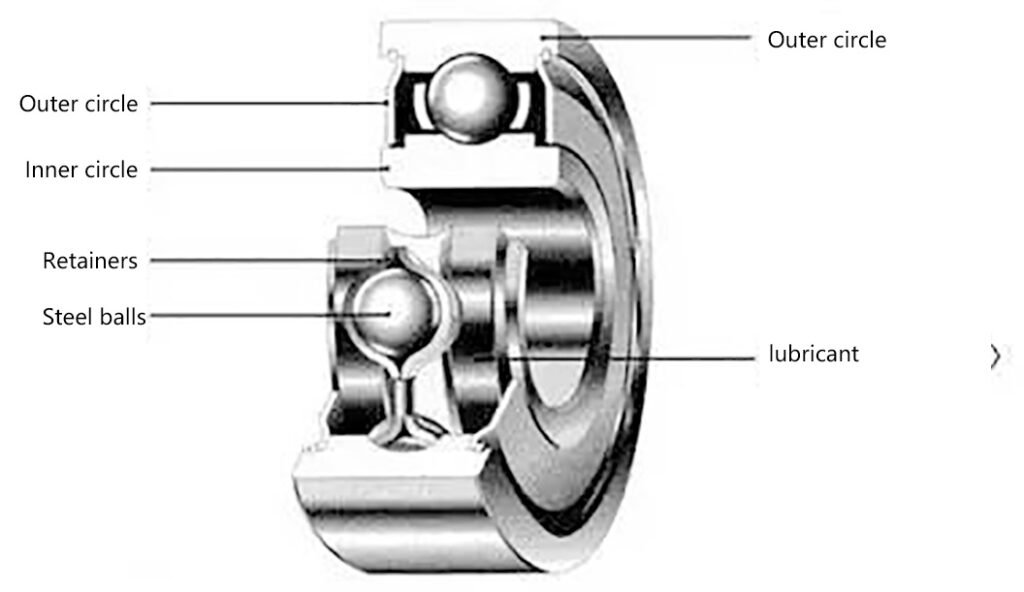
To maximize the performance and lifespan of a bearing, it is important to select the right type based on operating conditions. When choosing a bearing, consider the following factors:
- Radial load
- Axial load
- Speed requirements
- Radial runout
- Axial runout
- Operating temperature
- Noise requirements
- Lubrication conditions
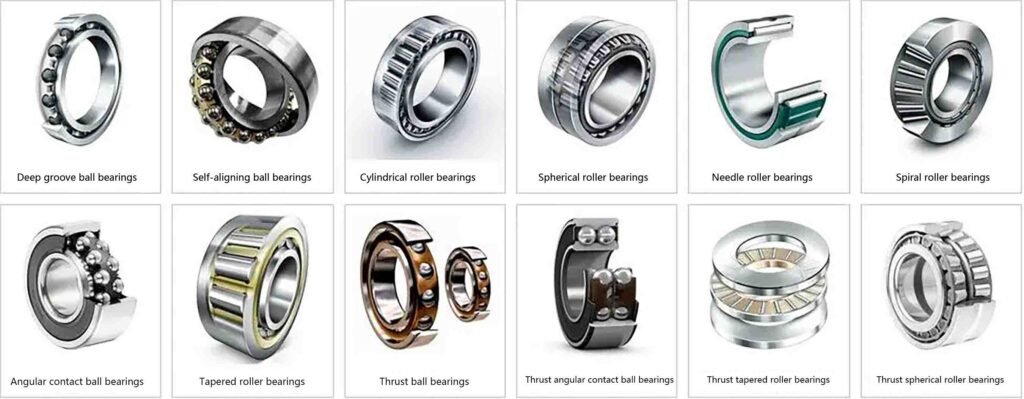
I. Bearing Code
The bearing model typically consists of a prefix code, basic code, and suffix code. Generally, the model is represented by the basic code alone. The basic code usually includes three parts: type code, dimension series code, and bore diameter code. The suffix code, expressed by letters and numbers, indicates the bearing’s structure, tolerance, and special material requirements. The prefix code represents bearing components and is denoted by letters.
The standard bearing (rolling bearing) code method includes a prefix code, basic code, and suffix code.
II. Basic Code
The basic code indicates the bore diameter, diameter series, width series, and type. It typically consists of up to five digits. Here’s a breakdown:
- The bearing’s bore diameter is indicated by the last two digits of the basic code. For commonly used diameters between 20 mm and 480 mm, the bore size is a multiple of 5. The two digits represent the result of dividing the bore size by 5. For example, 04 indicates d = 20 mm, and 12 indicates d = 60 mm. For bore diameters of 10 mm, 12 mm, 15 mm, and 17 mm, the codes are 00, 01, 02, and 03, respectively. For diameters smaller than 10 mm or larger than 500 mm, different rules apply. You can refer to GB/T272-93 for details.
- The diameter series, which represents variations in the outer diameter and width of bearings with the same structure and bore, is indicated by the third digit from the right in the basic code. For radial and radial-thrust bearings, 0 and 1 indicate extra light series, 2 is light series, 3 is medium series, and 4 is heavy series. Thrust bearings use similar codes, with 1 indicating extra light series.
- The width series, representing variations in width for bearings with the same structure, bore, and diameter series, is indicated by the fourth digit from the right in the basic code. For most bearings, the 0 series width (normal width) is not specified in the code. However, for spherical roller bearings and tapered roller bearings, the width series code 0 must be included. The diameter and width series codes are collectively called the dimension series code.
- The type code is indicated by the fifth digit from the right in the basic code (or a letter for cylindrical roller bearings, needle roller bearings, etc.).
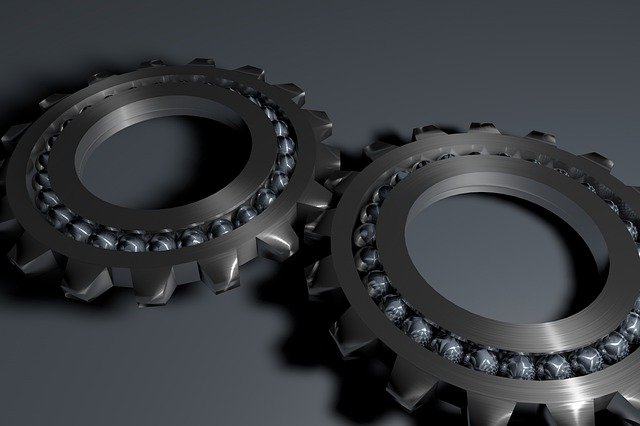
III. Suffix Code
The suffix code, consisting of letters and numbers, indicates the bearing’s structure, tolerance, and special material requirements. Commonly used suffix codes include:
- Internal structure code: This indicates different internal structures of the same type of bearing, represented by letters after the basic code. For example, angular contact ball bearings with contact angles of 15°, 25°, and 40° are represented by C, AC, and B, respectively.
- Tolerance grade: Bearings have six grades of tolerance: PZ, P4, PS, P6, P6X, and PO, listed from highest to lowest precision. Grade 6X is used only for tapered roller bearings, while grade 0 is the standard grade and not shown in the bearing code.
- Radial clearance: Bearings have six clearance groups: CI, CZ, C3, C4, CS, and 0, from smallest to largest clearance. Group 0 is the standard clearance and is not displayed in the bearing code, while the others are marked in the code.
Ⅳ.Prefix Code
The prefix code represents bearing components and is denoted by letters. For example, L indicates separable rings for separable bearings, and K indicates rolling elements with cages.
There are many types of rolling bearings in practical use, and the corresponding bearing codes can be complex. The codes introduced above are the most basic and commonly used. Familiarity with these codes will help you identify and select common bearings. For detailed bearing code information, refer to GBT272-93.
Ⅴ.Bearing Selection Method
Market demands for mechanical devices and instruments using rolling bearings are becoming stricter, and the performance requirements for bearings are increasingly diverse. To select the most suitable bearing from the numerous available structures and sizes, various factors must be considered.
When selecting bearings, generally consider bearing arrangement, ease of installation and removal, available space, bearing dimensions, and market availability. This helps determine the bearing structure. Then, compare the machine’s design lifespan with different bearing endurance limits to decide on the bearing size.
Often, the focus is on bearing fatigue life, but it’s also important to consider lubricant life, wear, noise, and other factors related to grease aging. Additionally, special bearings may be needed for specific applications requiring precision, clearance, cage structure, and lubrication.
There is no fixed rule for selecting bearings. The priority is to consider the most relevant performance and conditions required for the bearing in practical applications.
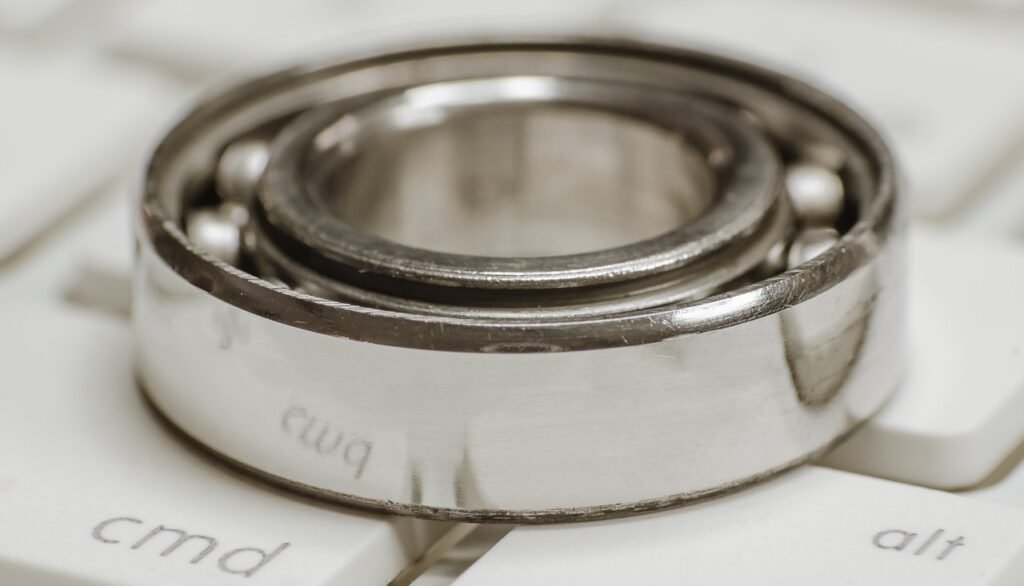
Ⅵ. Bearing Usage Guidelines
Rolling bearings are precision components and should be handled with care. Even high-performance bearings may not perform well if not used properly. Here are some key points to ensure proper use:
- Keep the bearing and its surroundings clean. Even small dust particles can harm the bearing, so it’s important to maintain cleanliness and prevent dirt from entering.
- Handle bearings with care. Strong impacts can cause dents and scratches, leading to bearing failure. In severe cases, it can cause cracks or fractures.
- Use the correct tools. Avoid using makeshift tools and always use the appropriate equipment for bearing handling.
- Prevent rust. Sweat on hands can cause bearings to rust. Always handle bearings with clean, dry hands, and wearing gloves is recommended.
Ⅶ.Proper Bearing Installation
Correct installation affects the bearing’s precision, life, and performance. The design and assembly departments should carefully study the installation process, following standard procedures. The standard steps include:
- Clean the bearing and related components.
- Check the dimensions and finish of related parts.
- Install the bearing.
- Inspect the installed bearing.
- Lubricate the bearing.
Before installation, unpack the bearing. For grease-lubricated bearings, do not wash them; simply apply the grease. For oil-lubricated bearings, cleaning is usually unnecessary, except for instrument or high-speed bearings, which should be cleaned with clean oil to remove any rust inhibitors. Once cleaned, bearings are prone to rust and should not be left unprotected. Pre-greased bearings do not require cleaning and can be used immediately.
The installation method varies based on the bearing structure, fit, and conditions. Generally, since the inner ring rotates, an interference fit is needed. Cylindrical bore bearings are often pressed in using a press or installed by heating. Tapered bore bearings can be mounted directly on tapered shafts or using sleeves. For housing installation, a clearance fit is usually required, and the outer ring is typically pressed in, or in some cases, a shrink fit is applied by cooling the bearing before installation. When using dry ice as a coolant, moisture in the air can condense on the bearing surface, so rust prevention measures are necessary.
Ⅷ. Bearing Maintenance
To maintain the original performance of bearings for as long as possible, regular maintenance and inspections are essential to prevent accidents and ensure reliable operation. Maintenance should follow standard procedures based on the operating conditions. This includes monitoring the operating state, replenishing or replacing lubricants, and periodic disassembly for inspection. During operation, you should monitor bearing noise, vibration, temperature, and lubricant condition.
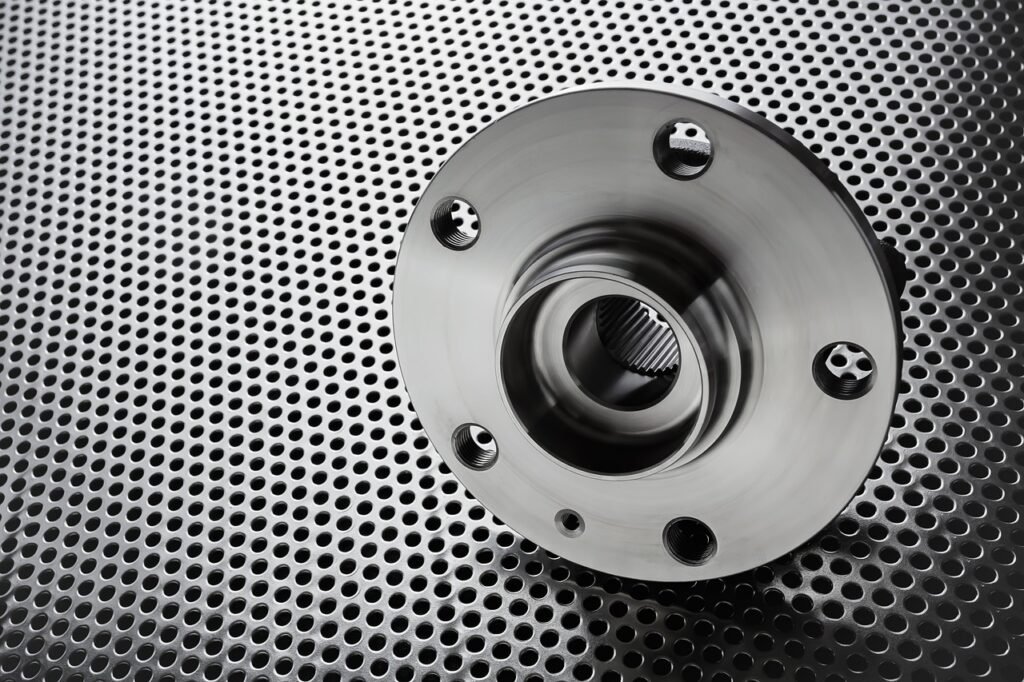
Ⅸ.Bearing Lubrication
The purpose of lubricating rolling bearings is to reduce internal friction and wear, and prevent overheating. Proper lubrication provides the following benefits:
- Reduces friction and wear by preventing metal-to-metal contact between rings, rolling elements, and cages.
- Extends fatigue life. Good lubrication on rolling contact surfaces increases the bearing’s fatigue life, while low oil viscosity or poor lubrication shortens it.
- Removes frictional heat and cools the bearing. Lubricating oil can carry away heat generated by friction or external sources, preventing overheating and degradation of the oil.
- Prevents contaminants from entering the bearing and helps protect against rust and corrosion.
There are two main lubrication methods: grease lubrication and oil lubrication. The choice depends on the bearing’s operating conditions and application. Oil lubrication generally provides better performance, but grease lubrication simplifies the surrounding structure. Both methods have their pros and cons, which should be compared.
X.Bearing Inspection Methods
Cleaning the Bearing: When disassembling a bearing for inspection, first record its external appearance and check the remaining lubricant. Take a sample of the lubricant for analysis, then proceed to clean the bearing. Cleaning agents such as kerosene or specialized bearing cleaners are commonly used. The cleaning process consists of rough and fine cleaning. Place the bearing in a container with a metal grid at the bottom to avoid direct contact with dirt. During rough cleaning, do not rotate the bearing with dirt on it, as this may damage the rolling surfaces. Use a brush to remove grease and debris before fine cleaning, where the bearing is carefully cleaned while rotating in clean oil. The cleaning oil must be kept clean during the process.
Inspection and Judgment:
After cleaning the bearing, inspect the raceways, rolling surfaces, mating surfaces, and cage for wear, increased bearing clearance, and any damage or irregularities that may affect precision. For small non-separable ball bearings, support the inner ring horizontally with one hand and rotate the outer ring to check for smooth rotation. For separable bearings like tapered roller bearings, inspect the rolling elements and raceways separately. Larger bearings cannot be manually rotated, so carefully inspect the rolling elements, raceways, cages, and flanges. The more critical the bearing, the more thorough the inspection should be.
Contact us for expert support in custom machined parts. We’re dedicated to delivering high quality, precision, and quick turnaround for your projects.