Plastics can be categorized by their long-term usage temperatures into three main groups: general-purpose plastics, engineering plastics, and high-temperature engineering plastics. High-temperature plastics are also known as heat-resistant plastics, high-performance plastics, or specialty engineering plastics.
General-purpose plastics have a long-term usage temperature below 100°C. This group includes PE, PP, PS, PVC, and ABS. General-purpose plastics are the most commonly used in daily life. They are typically used for packaging, household items, toys, and more.
Engineering plastics have a long-term usage temperature between 100°C and 150°C. The five main engineering plastics are PA, POM, PBT, PC, and PPO. These plastics are often used in mechanical parts, automotive components, and electrical applications.
High-temperature engineering plastics can be used at temperatures above 150°C. In addition to high heat resistance and flame retardance, these materials often exhibit excellent machinability, aging resistance, dimensional stability, and outstanding electrical properties. They can replace metal materials and find applications in electronics, aerospace, medical devices, automotive, and military fields. High-temperature engineering plastics represent the pinnacle of plastic materials.
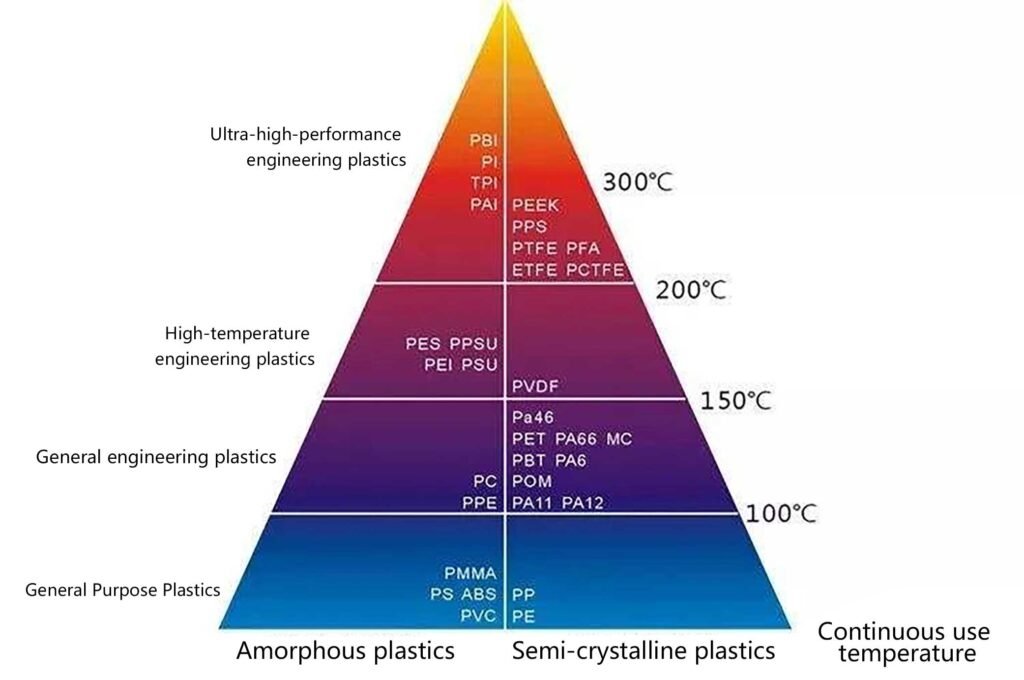
Ⅰ.High-Temperature Nylon
High-temperature nylon is divided into three categories:
1. Aliphatic Nylon — PA46
PA46 is an aliphatic polyamide made from the condensation of hexamethylenediamine and adipic acid. Compared to PA6 and PA66, PA46 has more amide groups per given length of chain. Its chain structure is more symmetrical, allowing for a crystallinity of up to 70% and a very fast crystallization rate. PA46 has a melting point of 295°C. The unreinforced heat distortion temperature (HDT) of PA46 is 160°C, while glass-fiber-reinforced PA46 can reach an HDT of up to 290°C. Its long-term usage temperature is 163°C. The unique structure of PA46 provides properties unmatched by other materials.
PA46 is mainly used in electronics, aerospace, and automotive applications.
Example Applications:
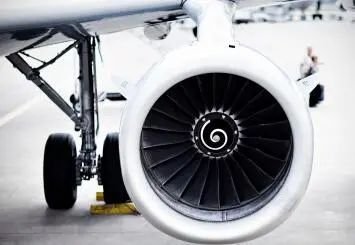
DSM's 30% glass-fiber reinforced PA46 is used in aircraft engine liners.
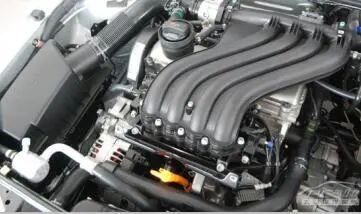
DSM's 40% glass-fiber reinforced PA46 is used in automotive intake manifolds.
2. Semi-Aromatic Nylon — PPA
PPA is made from the condensation of aromatic dicarboxylic acids and aliphatic diamines. Its melting point ranges from 310°C to 325°C, and its heat distortion temperature is between 280°C and 290°C. Common types include PA4T, PA6T, PA9T, and PA10T.
Compared to standard PA66, PPA has a very low water absorption rate. Even after soaking in cold water for years, its tensile strength remains over 80%. PPA also exhibits excellent oil resistance, maintaining high resistance to lubricants and fuels at elevated temperatures. Additionally, PPA provides excellent dimensional stability and weather resistance.
PPA is commonly used in automotive, electrical, mechanical, and consumer goods industries.
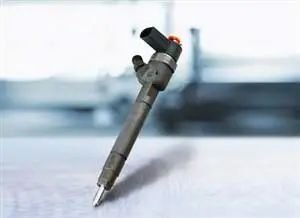
Automobile fuel injector
3. Fully Aromatic Nylon — PARA
PARA is invented by DuPont. The most famous examples are Nomex (meta-aramid) and Kevlar (para-aramid). These materials are primarily used to produce high-performance fibers and sheets. The fibers made from PARA exhibit high strength, rigidity, modulus, heat resistance, and dielectric strength.
PARA can be applied in ultra-strong fibers and composite materials for military, aerospace, and structural components.
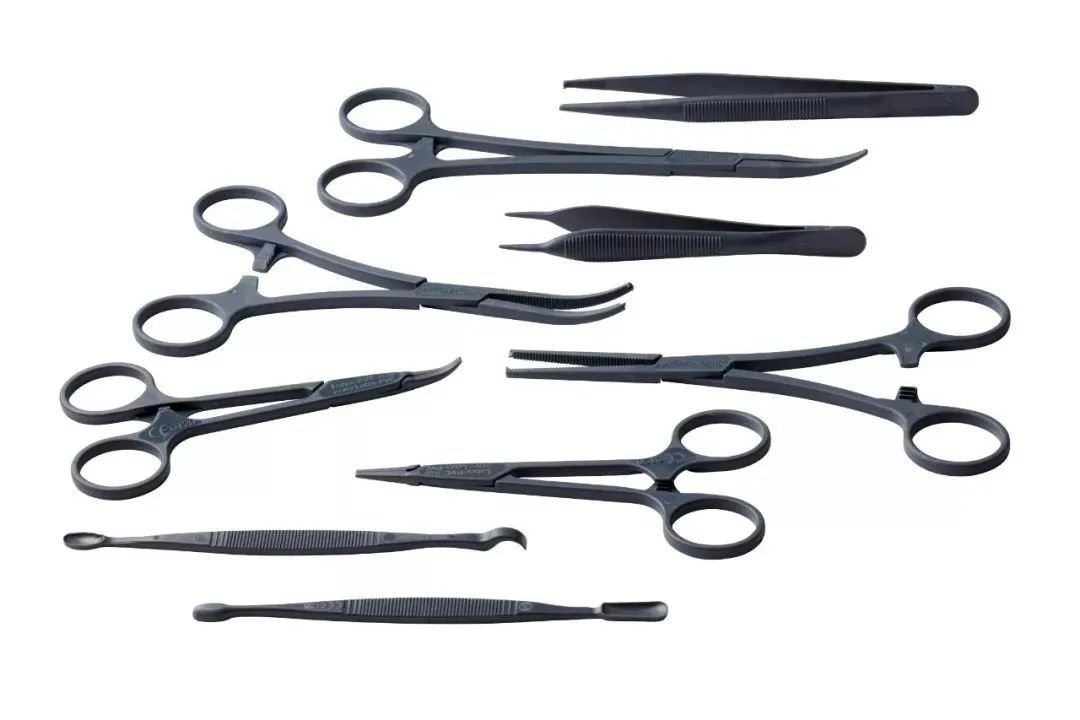
Solvay PARA for disposable surgical instruments
Ⅱ.Polyphenylene Sulfide (PPS)
Polyphenylene sulfide (PPS) is one of the fastest-growing and most widely used specialty engineering plastics. It offers excellent high-temperature resistance, chemical resistance, weather resistance, flame retardance, and electrical properties. Its dimensional stability is also outstanding. PPS is widely used in automotive, electrical, mechanical, petrochemical, pharmaceutical, light industry, military, aerospace, and 5G communication sectors. It is the most commonly used specialty engineering plastic.
PPS is also the most domestically produced specialty engineering plastic in China, with a self-sufficiency rate exceeding 80%. According to incomplete statistics, major global PPS manufacturers have a total capacity of over 200,000 tons. Currently, PPS production capacity is mainly concentrated in Japan and China.
Leading traditional PPS companies, such as DIC, Toray, Solvay, and Wu Yu, remain ahead in production and technology. Together, their combined capacity accounts for over 56% of global production. However, Chinese companies are rapidly emerging. Domestic firms like Zhejiang Xinhacheng and Chongqing Jushi have begun large-scale production, and several other companies are either in mass production or planning to enter the market.
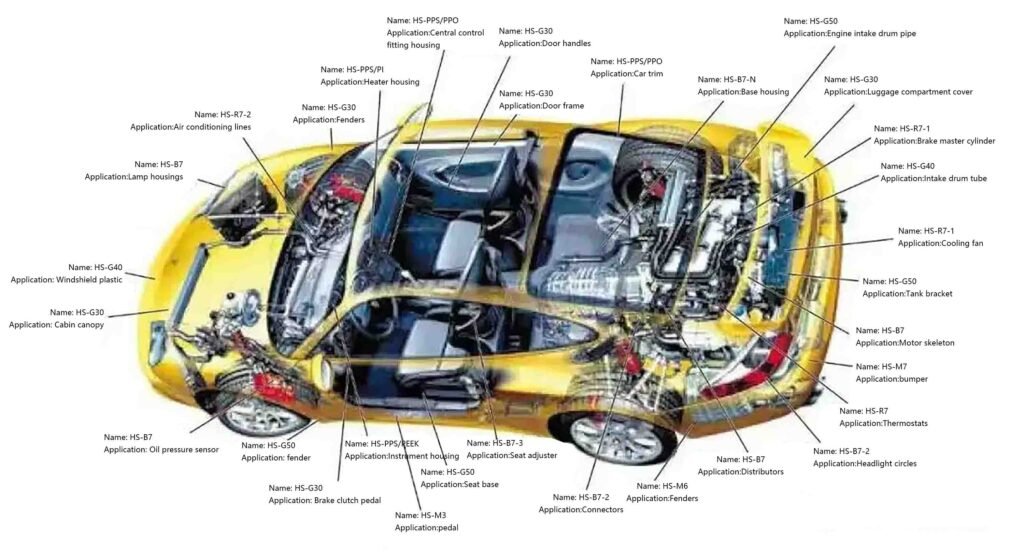
Ⅲ.Polyaryletherketone (PAEK)
Polyaryletherketone (PAEK) is a polymer with a backbone made of phenyl rings connected by ether and ketone bonds. It can be categorized into several types based on the number and arrangement of ether and ketone groups: Polyether Ether Ketone (PEEK), Polyether Ketone Ketone (PEKK), Polyether Ketone (PEK), and Polyether Ketone Ether Ketone Ketone (PEKEKK).
1. PEEK (Polyether Ether Ketone)
PEEK is a specialty engineering plastic with excellent overall performance. It exhibits outstanding heat resistance, water resistance, solvent resistance, and electrical insulation. Its fatigue strength is high, and it has the best radiation resistance among all plastics. PEEK has a high oxygen index, producing less smoke and no toxins when burned.

PEEK artificial bones
2. PEK (Polyether Ketone)
PEK has a lower ratio of ether and ketone groups compared to PEEK. As a result, its melting point and glass transition temperature are higher than those of PEEK. PEK offers superior heat resistance, with a continuous usage temperature of 250°C.
3. PEKK (Polyether Ketone Ketone)
PEKK is a high-performance material with a melting point ranging from 300°C to 600°C. It has strong chemical resistance and wear resistance. Recently, PEKK has seen rapid advancements in 3D printing applications, outperforming traditional 3D printing materials.
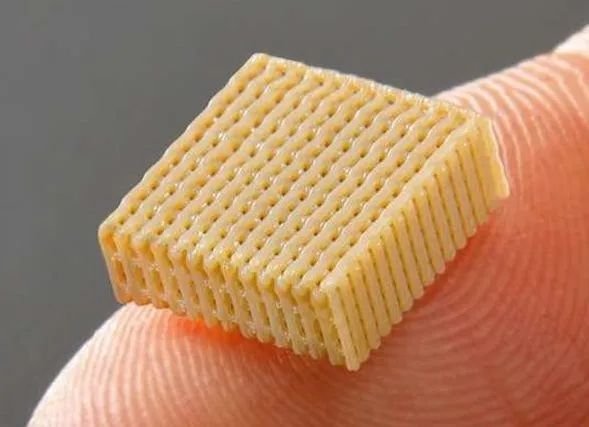
Milling Machining Methods
- Basic Milling: Includes plane milling, slot milling, side milling, and contour milling.
- Advanced Milling: Includes ramp milling, thread interpolation, trochoidal milling, push-pull contour milling, slotting, contour parallel milling, drilling.
Ⅳ.Polyimide (PI)
Polyimide (PI) is a high-performance polymer containing imide functional groups in its molecular structure. It is one of the best heat-resistant engineering plastics available today. PI can withstand extreme temperatures, with a thermal decomposition temperature reaching 600°C. It remains intact even at -269°C in liquid helium. Additionally, it offers excellent mechanical properties, acid and alkali resistance, biocompatibility, and electrical performance.
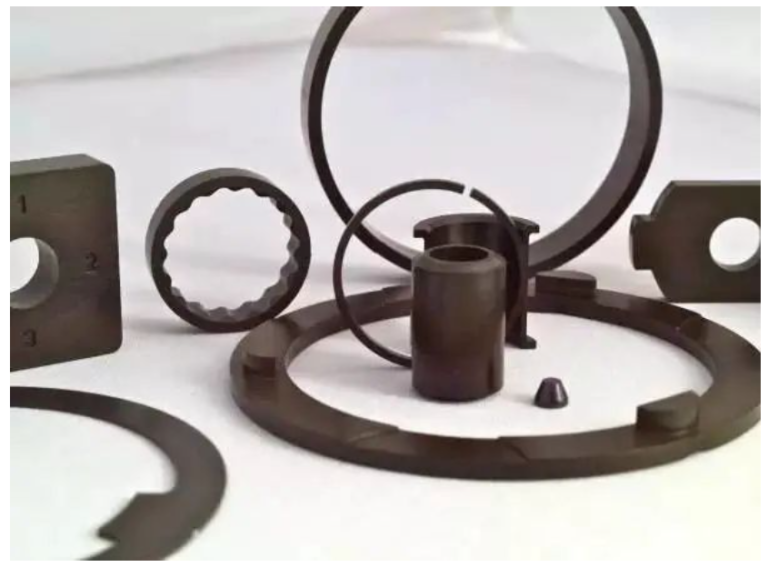
Polyimide engineering plastics can be both thermosetting and thermoplastic. They can be categorized into several types, including Poly(m-phenylene isophthalamide) (PMMI), Polyetherimide (PEI), and Polyamide-imide (PAI). Each type has specific applications in various fields.
PMMI
can achieve a heat distortion temperature of 360°C under a load of 1.8 MPa. It also exhibits excellent electrical properties. PMMI is suitable for precision parts used under special conditions, including high-temperature self-lubricating bearings, sealing rings, and blower impellers. It is also used in valve components that come into contact with liquid ammonia and in jet engine fuel supply system parts.
PEI
provides outstanding mechanical properties, electrical insulation, radiation resistance, high-temperature resistance, and wear resistance. Its excellent melt flow allows for easy injection and extrusion molding, with a shrinkage rate of 0.5% to 0.7%. PEI can be welded with other materials and is widely used in electronics, aerospace, automotive, and medical devices.
PAI
has the highest strength among non-reinforced plastics, with a tensile strength of 190 MPa and a bending strength of 250 MPa. Its heat distortion temperature reaches 274°C under a load of 1.8 MPa. PAI exhibits good ablation resistance and electromagnetic properties at high temperatures and frequencies. It bonds well with metals and other materials. PAI is primarily used in gears, bearings, and copier separation claws, as well as in ablation materials and structural components for aircraft.
Ⅴ.Polysulfone (PSU)
Polysulfone (PSU) is a slightly amber, amorphous, transparent, or translucent polymer. It has excellent mechanical properties, high rigidity, wear resistance, and high strength. Even at elevated temperatures, PSU maintains its outstanding mechanical performance. Its operational range is from -100°C to 150°C, with a long-term usage temperature of 160°C and a short-term usage temperature of 190°C.
PSU includes several types, such as standard Bisphenol A PSU, Polyphenylsulfone (PPSU), and Polyethersulfone (PESU).
1. Standard Bisphenol A PSU
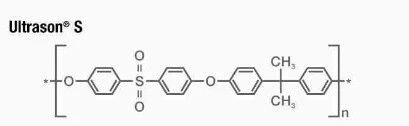
The conjugated effect of the sulfone group provides oxidation resistance and thermal stability. The ether chain enhances toughness, while the phenyl rings ensure mechanical strength and modulus.
2. Polyphenylsulfone (PPSU)
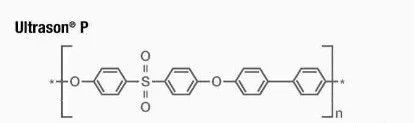
The phenyl rings in the main chain provide high heat resistance and mechanical performance. The ether bonds contribute to excellent flow properties and processing capabilities.
3. Polyethersulfone (PESU)
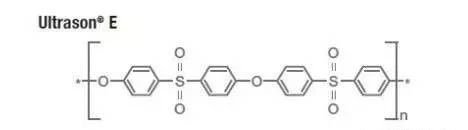
The ether groups provide flexibility and high flowability, while the sulfone groups ensure heat resistance. The phenyl rings contribute to rigidity.
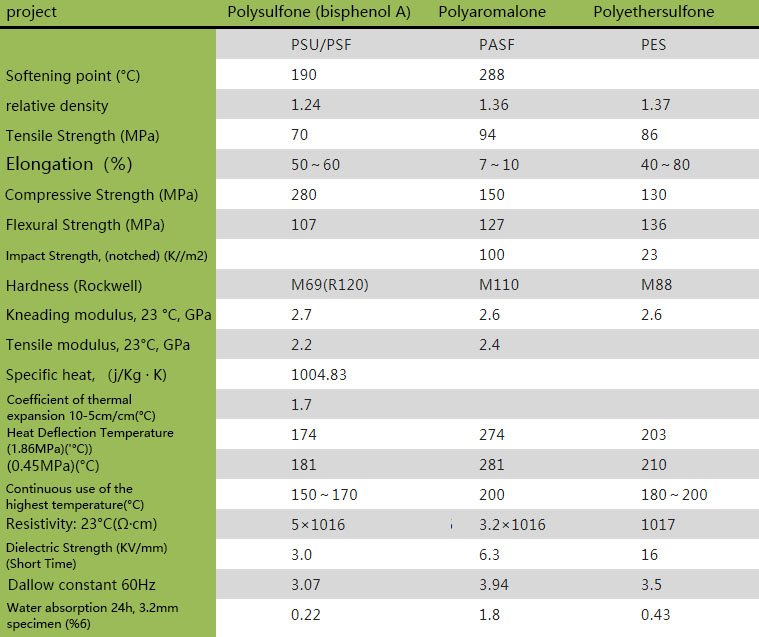
Comparison of the properties of bisphenol A type polysulfone, polyarylsulfone and polyethersulfone
Ⅵ. Polyarylate (PAR)
Polyarylate (PAR) is a thermoplastic resin that contains aromatic rings and ester bonds in its main chain. PAR exhibits excellent light transmittance, with a transparency of nearly 90%. It also has good toughness, heat resistance, elastic recovery, weather resistance, and flame retardance. Its continuous usage temperature can reach up to 170°C. PAR is primarily used in precision devices, automotive applications, medical fields, food packaging, and everyday consumer goods.
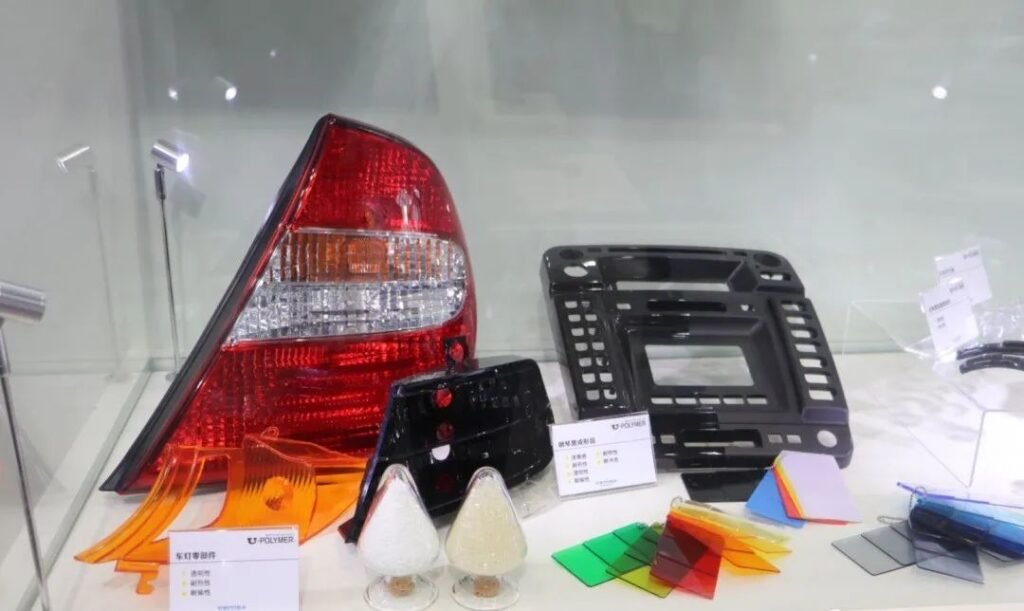
The structure of PAR is similar to that of polycarbonate (PC), and their performance characteristics are generally comparable. They can share molds for manufacturing. However, the higher density of aromatic rings in PAR improves its heat resistance compared to PC. PAR has a heat distortion temperature that is 20 to 40°C higher than that of PC, along with excellent UV resistance and creep resistance. However, its elongation at break and impact resistance are lower than those of polycarbonate.
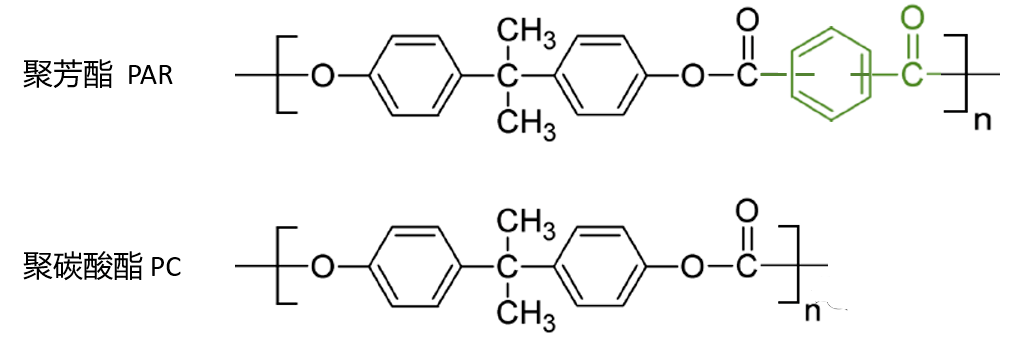
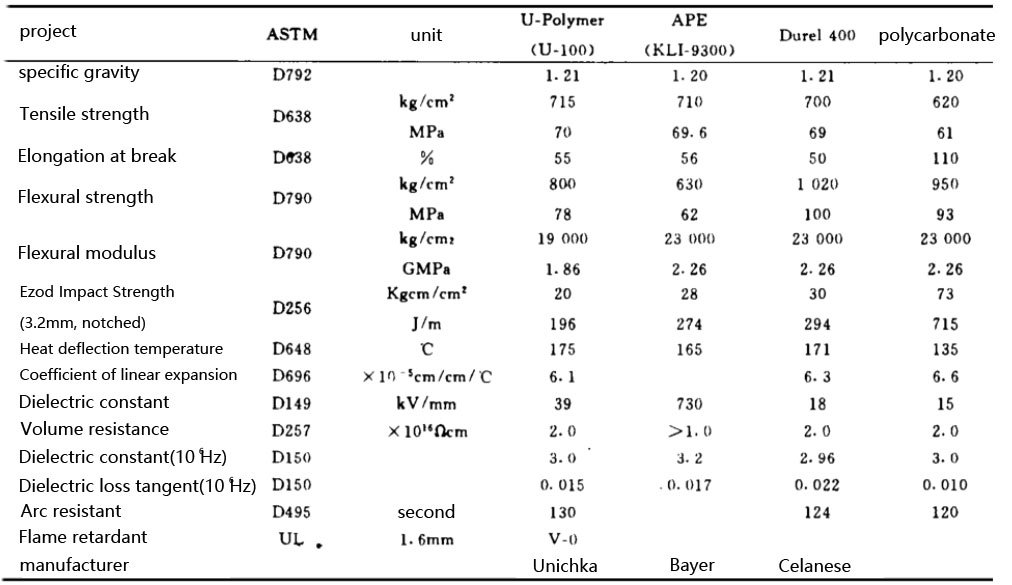
Performance comparison between PAR and PC
Ⅶ.Liquid Crystal Polymer (LCP)
Liquid Crystal Polymer (LCP) is a type of liquid crystalline compound. The term “liquid crystal” refers to substances that possess fluidity in a molten state while maintaining an ordered molecular arrangement like a crystal.
LCPs offer outstanding mechanical properties, with a unique characteristic: as the wall thickness decreases, their relative strength increases.
LCPs also have good thermal performance, with continuous usage temperatures ranging from 200°C to 300°C.
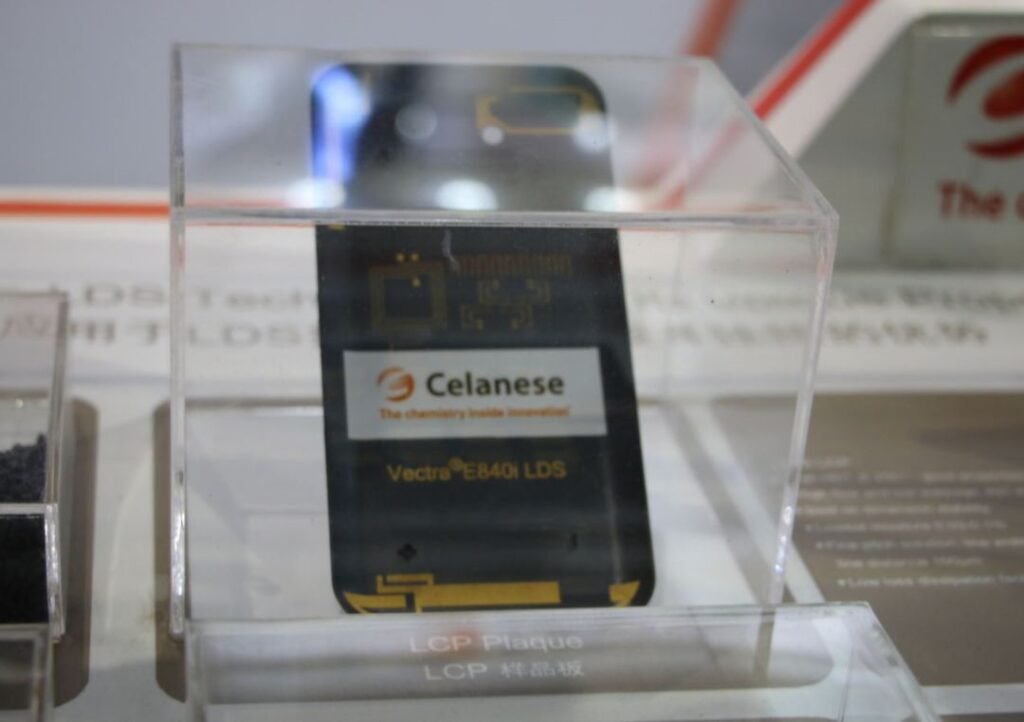
Their low dielectric constant and dielectric loss make them suitable for electronic devices, such as connectors, slots, switches, supports, and sensors. One of the most researched applications is in 5G antennas for mobile phones.
Ⅷ.Fluoropolymers
Fluoropolymers refer to plastics made from fluorine resins. The main types include Polytetrafluoroethylene (PTFE), Ethylene-Tetrafluoroethylene Copolymer (ETFE), Perfluoroalkoxy (FEP), and Polyvinylidene Fluoride (PVDF). These materials can operate at temperatures ranging from 150°C to 260°C.
Contact us for expert support in custom machined parts. We’re dedicated to delivering high quality, precision, and quick turnaround for your projects.